The idea of having a checklist, a comprehensive list of items to consider before beginning work, is probably one of the single most effective methods to ensure the safety of workers and property. When employees find themselves doing unfamiliar tasks, or doing routine tasks in an unfamiliar environment, a job hazard analysis (JHA) is widely used to identify and analyze the associated hazards. Even performing a familiar activity can bring about new and unknown hazards if it’s done under unique conditions or in unfamiliar places. It is crucial to account for the surrounding environmental conditions, the location and any unique circumstances of the environment for a JHA to be effective.
A comprehensive JHA does not have to be reinvented for every event. The main components and steps of a particular task can be documented in a way to allow the end user to adapt them to the environment. This allows the employee to focus on the unique hazards of the present environment and to incorporate safeguards to protect employees and property while ensuring that the routine task is done safely.
A great example of this is the modern incarnation of the pre-flight checklist. The idea of a comprehensive pre-flight analysis was first introduced at the Boeing Company following the 1935 crash of a Boeing B-17 in Dayton, Ohio that killed both pilots. The investigation found that the pilots had forgotten to disengage the gust locks which stop control surfaces from moving in the wind while parked. The idea of the pre-flight checklist/hazard analysis has evolved to consider weather and environmental conditions and is arguably one of the main reasons that modern commercial aviation is considered the safest method of travel.
During World War 2, following several incidents of munitions exploding in factories, the process of documenting and standardizing procedures was introduced to British munition factories. Companies proposing to supply the military with munitions had to submit their own process and procedures for evaluation. These documented programs were then used by inspectors to ensure employees were following procedures, therefore maintaining a safe work environment and preventing losses. It was soon realized that a byproduct of this process of standardizing procedures resulted in a product of consistent quality. This concept continued to evolve into what is now known as the International Organization for Standardization or ISO (derived from the Greek isos meaning equal). Today, many companies use the ISO framework to ensure the safe delivery of products of consistent quality.
When I was in the private sector, we sought ISO 9001 as the basis for a quality management system. Every aspect of virtually every job was documented with procedures and work instructions. This included remote employees on site at chemical plants, refineries and research facilities. When we would do a JHA, we would reference the specific procedures or work instructions for that task. I would often challenge employees to find something that was not documented.
So how does this translate to the public sector to prevent losses? Start small, perhaps look at where employee injuries are most often happening. Is there a high frequency of slips, trips and falls in a maintenance shop? You could implement a process to clean the area at the end of each workday and inspect it at the beginning of the workday to ensure that slip and trip hazards are mitigated. You could audit the program by requiring documentation that cleanup and inspections are taking place.
Even everyday tasks can cause big losses. Perhaps an employee hanging a picture puts a nail through the sheetrock, puncturing a water line to the ice maker in the adjoining room causing extensive water damage. Perhaps they put that nail through the 220V electric line supplying the ice maker? A JHA form asking if they are penetrating any surfaces that could have water or electric seems simple, but it goes a long way to ensure the employee takes these hazards into consideration.
For any risk control program, it’s important to pause and reflect on what could go wrong and incorporate steps to prevent or mitigate that possibility. Developing these habits takes time. Don’t get discouraged, start small, stay consistent and you’ll see the fruits of your labor.
*The views and opinions expressed in the Public Risk Management Association (PRIMA) blogs are those of each respective author. The views and opinions do not necessarily reflect the official policy or position of PRIMA.*
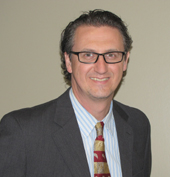
By: Patrick Durbin
Associate Director Risk Control, The University of Texas System
Summary of Qualifications
Patrick has 25+ years of experience in environmental, health and safety. He has 17 years' experience in risk control encompassing not only environmental, health, and safety, but also emergency management and business continuity. Patrick has over nine years' experience managing and navigating complicated claims involving property damage at multiple locations, business income losses and research losses, and 18 years experience working in the public sector.
Responsibilities
In his current role as associate director of risk control, Patrick is responsible at the corporate level for environmental, health, and safety, emergency management and business continuity, and all claims outside of workers' compensation. This includes a comprehensive training program that serves several hundred continuing education students every year, the property conservation program surveying over 100 buildings every year to support the property insurance program and self-insured retention, and coordinating and supporting the work of several systemwide committees and working groups focused on risk control programs throughout The University of Texas System.
Business Experience
Before his time with UT, Patrick worked in the private sector for a nationwide environmental service company that served several public sector entities including universities, cities, counties, and states, as well as many private sector companies including energy, oil and gas, chemical, and manufacturing. During his time in the field, Patrick managed crews working on site at many locations around the country, regularly interfacing with customers to ensure work was done in compliance with all applicable regulations while working within the bounds of budgets and contracts to meet customer and company expectations.
Moving from the field, Patrick became director of training and compliance which included developing and enhancing the training and safety programs for field and sales personnel, as well as developing site specific protocols for on-site personnel at several locations around the country. He also developed numerous ISO 9000 work instructions and procedures and was trained as an ISO auditor.
Professional Affiliations
- Certified Hazardous Materials Manager (CHMM)
- Certified Risk Manager (CRM)
- Current president of the local Central Texas Lone Star Chapter of the Alliance of Hazardous Materials Professionals
Education
Bachelor of Science in hydrology and water resources from Tarleton State University in Stephenville, Texas.